Operational Excellence Inc
Accelerating World Class Journeys
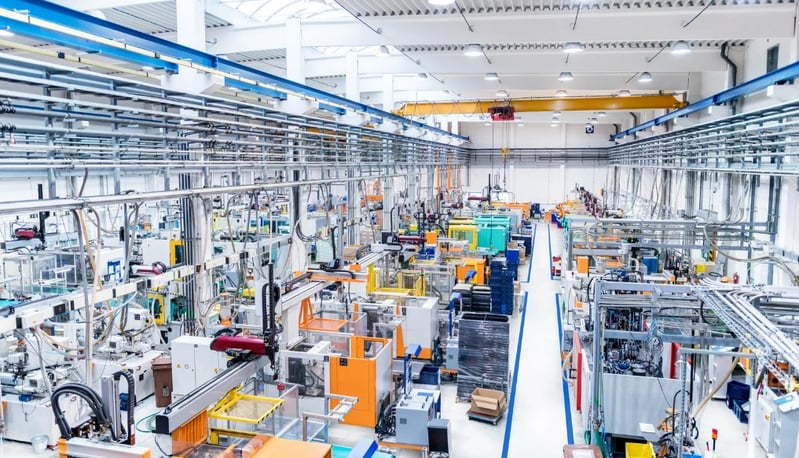
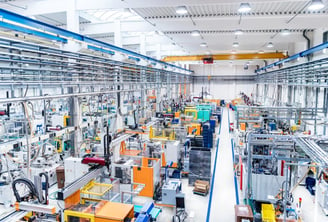
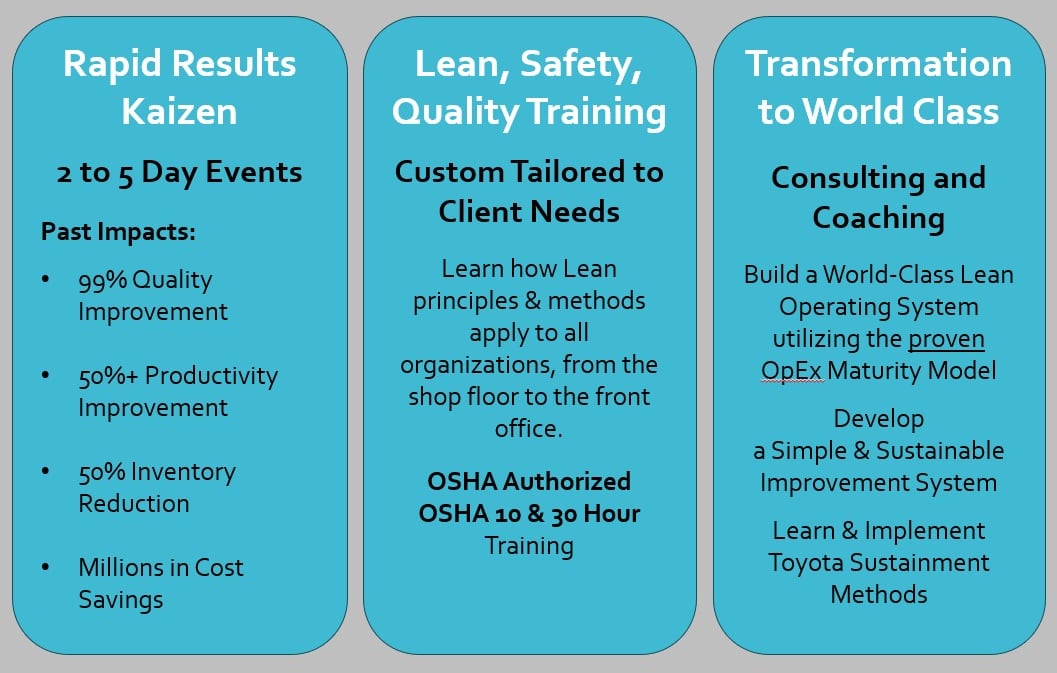
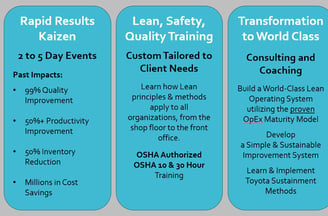
Clients choose the approach to meet their needs.
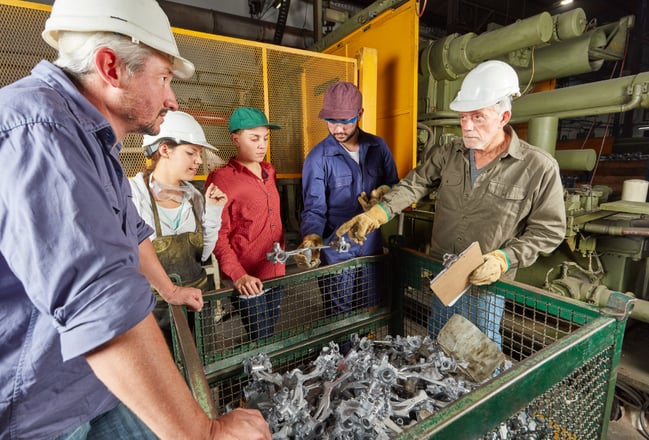
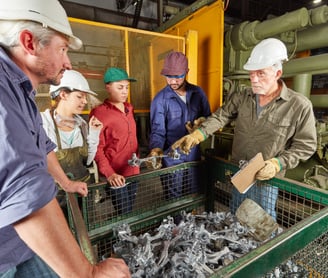
Rapid Results Kaizen
People who haven't participated in a Toyota Shop Floor Kaizen are generally shocked by how much can be accomplished in a very short time. Following the Toyota approach, the OpEx Inc facilitator harnesses the knowledge and abilities of the team to quickly achieve results.
Rapid Results Kaizen Workshops include:
5S & Visual Management
Value Stream Mapping
Standardized Work
Problem Solving
SMED Set-Up Reduction
Material Pull, Flow & Materials Management
Break-Through Built-In-Quality
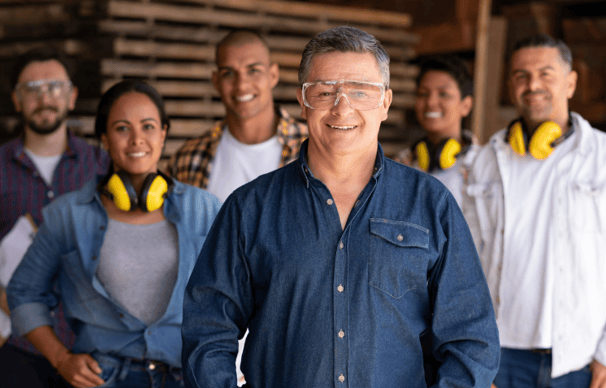
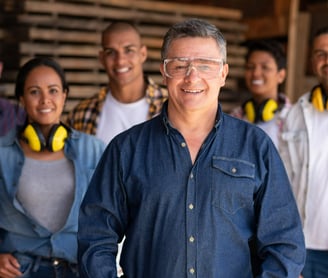
Lean, Quality & Safety Training
Lean Leaders know the importance of developing people. Teaching employees to recognize waste, fuels ideas to improve their processes. OpEx Inc provides Lean Introductory training designed for adult learners, including discussions, group activities, quizzes and some visits to the shop floor. Courses can be taken as part of a Rapid Results Kaizen, or as stand-alone training. Some of the courses offered are:
OSHA 10 & 30 Hour for General Industry
Introduction to Lean
Effective Communication & Teamwork
5S & Visual Management
Problem Solving
Standardized Work
Train the Job Skills Trainer
Built-In-Quality & Error Proofing
Total Productive Maintenance
Lean Leadership
Training workshops more than pay for themselves over time, if not immediately in kaizen workshops. Additionally, there are grants that can help make these workshops an exceptional value. Find more information here: https://nextleveljobs.org/employer/how-it-works/
Transformation to World Class
Executive Lean Transformation Leaders understand the difficulties of launching the lean journey without a team of experienced lean managers, and/or a highly skilled Change Agent. Prior to joining Toyota, Dane Bohnert started learning Lean at the Japanese auto parts supplier PKUSA, and then at PMC, where he was a member of the management team tasked with performing kaizens to reduce waste, with coaching from a Lean Change Agent. Later Dane joined the Indiana Toyota Truck & Van plant as a Supplier Development specialist, where he learned Toyota's approach to helping companies transform by utilizing Toyota assessments to set improvement targets. After leaving Toyota, Dane has had nearly 10 years of training and consulting experience, along with 8 years as Lean Change Agent for an American division of the Swiss-German process control tech company Endress & Hauser. For more than a decade, Dane has interwoven lessons learned as a Change Agent, with key elements of Toyota's supplier assessments to create the OpEx Inc Lean Maturity Model (LMM). The LMM provides clear and simple criteria to advance along a scale from Level 1 to Level 5 on various elements of the Toyota Production System. Utilizing the LMM, Toyota supplier development coaching methods, and his experience navigating the various challenges to the transformation, Dane is well prepared to help any organization make progress on the journey to World Class.
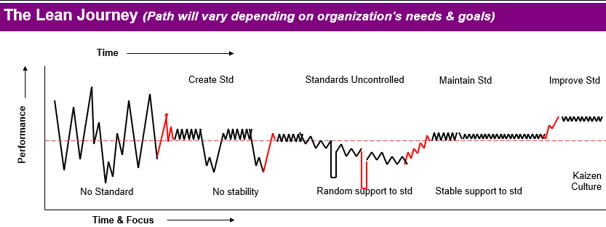
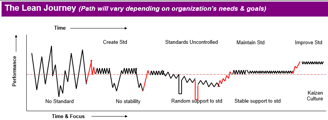
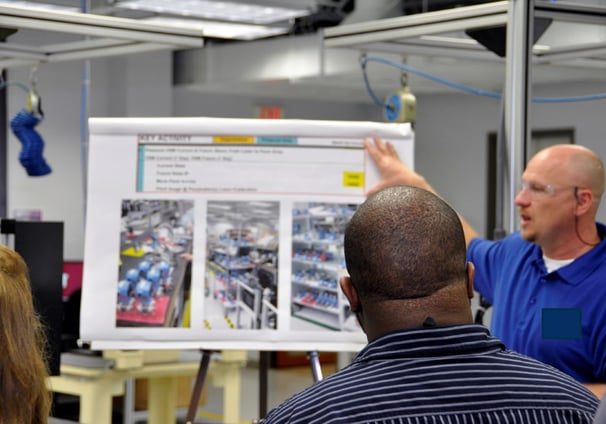
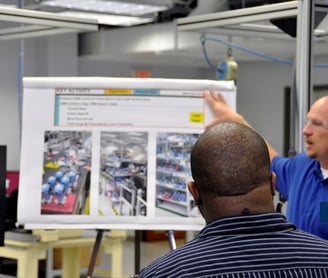
Improvement System Development
As once heard from a client, "We have a lot of experience with Problem Solving; we just keep solving the same problems." It is common for workplace processes and conditions to backslide after solutions are found.
There is no journey to world class without a solid Improvement System that spans from top leadership vision to implementation of ideas generated on the shop floor. OpEx has the proven experience to guide your leadership team through the steps to quickly create a simple, highly effective and sustainable improvement system. Once the basics are in place, we can work with your leaders to help it become a natural part of your company culture.
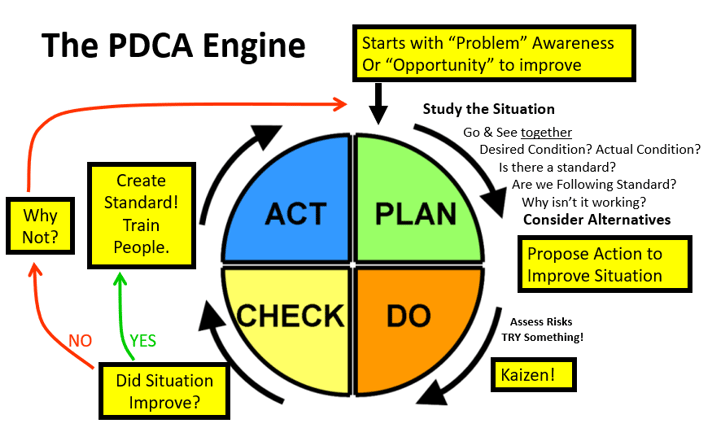
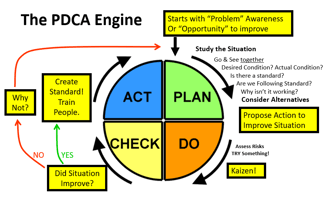